The Beginning of Mass-Producible LiDARs: An Interview with Hesai Technology CEO at CES 2022
LiDAR, which stands for Light Detection and Ranging, determines the range of objects with a laser pulse and measures how long it takes for the beam to be reflected. It is one of the primary and fastest-growing technologies used in the autonomous driving industry and has a market size of 1.3 billion as of 2021.
Hesai Technology, founded and based in Shanghai since 2014, specializes in LiDAR technology for autonomous driving and ADAS. As one of the leading companies in the industry, Hesai has showcased some of its newest high-performance, reliable, and low-cost 3D sensors expected to enter mass production by the time of CES 2022.
Pandaily sat down with David Li, CEO of Hesai, at CES to talk about the company and some of its highlights at the show this year.
· What went into the decision of founding the company, and why did you choose the LiDAR industry?
The founding of the company is a typical Silicon Valley startup story: you work at a big firm, you get bored, and too much certainty has become a negative factor. I happened to have two friends who were feeling the same way, so we decided to co-found the company.
By the time we decided to found the company, though, we hadn’t quite figured out what to work on. So we looked at what we were good at, and what we were interested in. It turned out that all of us were interested in hardware – tangible things that can move around. Today, you would call it robotics.
We also happened to be good at laser-related technology. One of our partners studied laser [technology] at Stanford, and all of us were interested in different applications of lasers. So that’s what we decided to do. About two years after the inception of the company, we found that lasers were very powerful in sensing in robotics: a direction we decided to pivot into in 2016, and it just turned out that most of the LiDAR companies today were founded at the same time.
· There has been a lot of talk about the idea of the mass production of LiDARs, especially in the past year. What would you say are the biggest challenges for the commercialization and mass production of LiDARs?
I’ll give you two versions of my answer. The official answer is that there has to be a good system for mass-producible designs that follow the automotive-grade standards. In the past, most companies were making high-quality samples in smaller quantities; but in the later stage of mass production, much bigger quantities are produced with the same level of quality. We’re talking about going from 10,000 units at best to easily a million units a year: it’s a huge leap there.
The unconventional answer is that, oftentimes, people think about quality as a problem of screening the bad ones. But it entails a lot more: it’s about designing something that’s durable in the first place, which is a very different topic. Just controlling the consistency of the product wouldn’t give you what you want without a good design. We have to constantly think about how we can have a LiDAR that’s mass-producible in the first place, which is a challenge that’s easily overlooked.
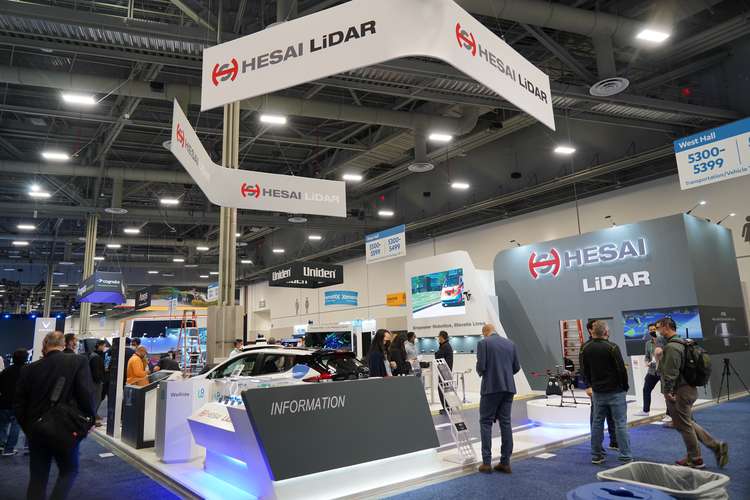
· We know that Hesai has been working on chip-based LiDARS – what led the company to invest so much in your proprietary LiDAR ASICs?
In my mind, ASICs are application-specific: it is about combining a large number of components into a small integrated part with a design that’s geared to serve a very specific application. In other words, the opposite of ASICs is a more general chip that will do everything. So one reason to do ASICs is that it’s tailored to your product’s need.
Another is that it’s highly integrated, sparing the process of assembling hundreds of parts into one. The ASICs design process is long, but afterwards, you will be able to enjoy the benefits of any printing process, where you can quickly, efficiently, consistently, and affordably duplicate everything off the shelf. This will take your competition to the next level.
Another benefit on top of this comes with Moore’s Law. The idea is if you keep making semiconductors denser and smaller, you’ll be able to halve the cost of any design on a chip every 18 months. So once you figure out how to move your design onto an ASIC, you are guaranteed to continuously halve your cost every 18 months. That’s very important for mass production, especially in the automotive industry, because it’s about performance, reliability, and above all, cost. ASICs, which give us the capability and architecture to support the continuous cost decline, is the best tool to deliver high-quality, high-consistency, and low-cost products.
· The highlight of Hesai at CES this year seems to be the latest AT128, which makes use of the ASICs technology. Could you tell us a bit more about this product and what are some of its applications?
The AT128 is a long-range, hybrid solid-state LiDAR for mass-produced passenger and commercial vehicles. The first important feature is its long detecting range, which goes as far as 200 meters. Another one is its point density resolution, going over 1.5 million points per second.
The uniqueness of our current AT product is the new generation of semiconductor technologies used to achieve their specs in each of the standard categories. We recently announced our collaboration with Lumentum, the company famous for making 3D sensors for iPhones, and we are the first to incorporate their consumer electronics technologies into long-range LiDARs. Our third-generation proprietary ASICs also allowed us to integrate all this onto just a few chips.
The AT128 was primarily designed for the ADAS (Advanced Driving Assistance) system and very easily integrated into the car body design, so we will be seeing it on the front bumper, roof, or sides of cars. But its application goes beyond this, since many other robotics manufacturers who didn’t consider using LiDARs in the past are now turning to LiDARs because of the reduced prices, and their products include drones, sweepers, and delivery robots. AT128 is high-performance and extremely affordable, and we believe that it would make a huge impact in the market.
Our company’s mission is to empower robotics. We don’t just make robots; instead, we want to build a platform for technologies that would empower a variety of new applications in robotics, including everything just mentioned and autonomous driving vehicles, which just happened to be robots with four wheels.
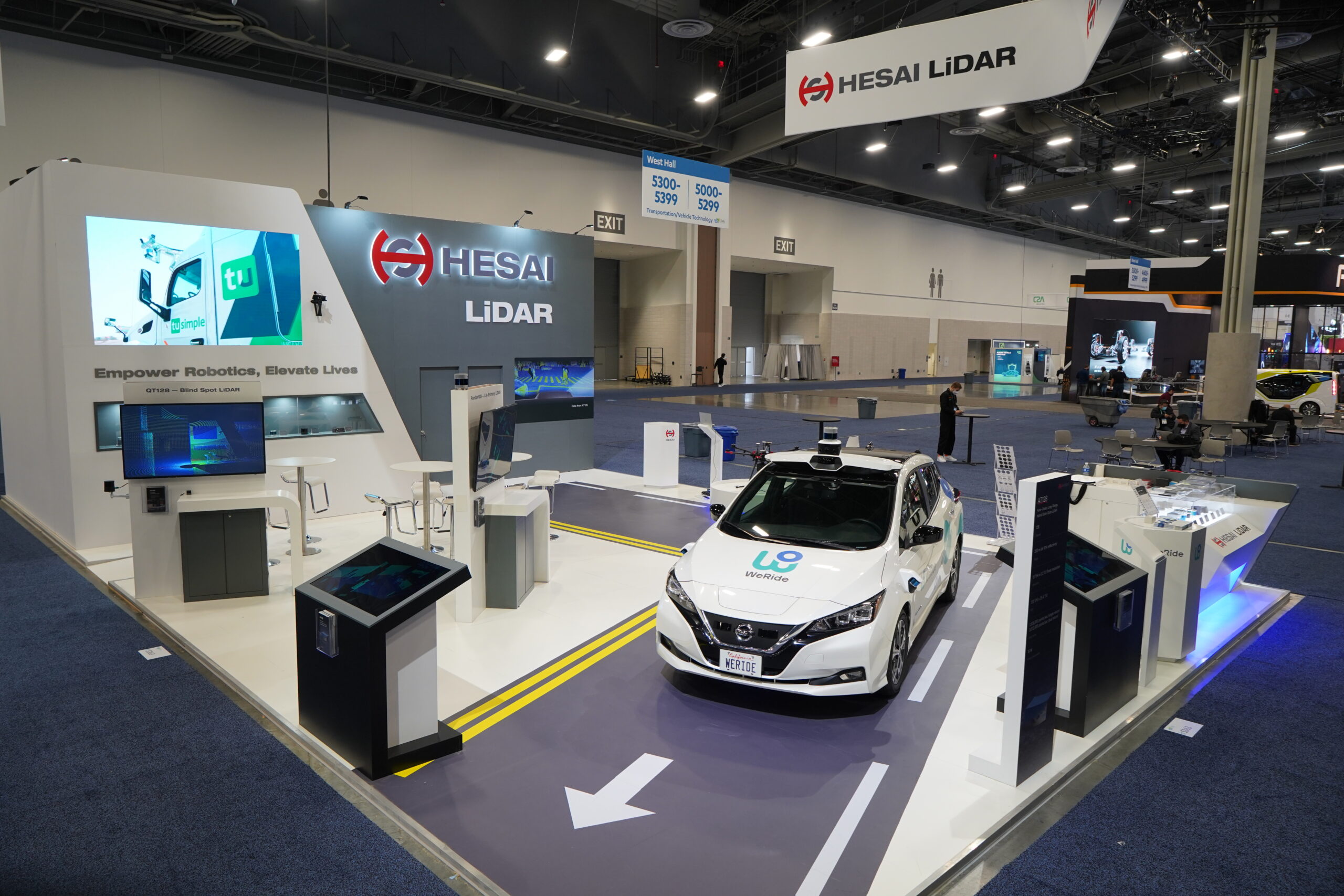
· Where do you see the LiDAR and autonomous driving industries going in the next 5 to 10 years?
I will make the bold prediction that LiDARs will evolve in a fashion similar to a camera, in that it is going to be smaller, cheaper, and less complex in structure. A camera gives you RGB, and a LiDAR gives you the fourth dimension – depth – that adds onto color sensing. In the end, it is even possible that everything will be combined into one single device under one mechanism.
As with robotics in general, there are so many more possibilities. New applications will occur in fields we have not imagined, just like the way we did not expect our phones to have all the functions they have now ten years ago. Once the platform is established, countless innovations will happen. This is why what we do is exciting: even though we are working on a small part of robotics, we are elevating the number of possibilities that will come in the industry in the future.
· What would you say to the LiDAR vs camera debate, when it comes to sensing in autonomous driving?
Even though LiDARs can be considered redundant by adding an additional dimension to the sensing process, this “redundancy” is usually a plus because it also enables an additional level of safety. Of course, the counterargument is that people believe that camera-based technologies are advancing so quickly that, in the end, it will catch up to the “camera plus LiDAR” approach, and the cost of LiDARs will not be justified.
To this, I would first say that for any AI machine, having additional trustworthy information is always helpful, so LiDAR plus camera will always be better than the camera alone. The question then becomes if the difference will be so small that the cost of LiDARs will be justified.
Let’s think about it, in the last ten years, the number of fatal accidents caused by camera-only systems that could have been prevented by the use of LiDAR. Today, this percentage is close to a hundred, but you would be surprised if it ever becomes one. Even in ten years, it is likely that the proportion will still be more than 50%, and it would make sense to say that cars with LiDARs will be twice as safe as those without. Even if the car is a few thousand dollars more expensive, I believe that consumers will still go with the option that doubles the safety margin.
SEE ALSO: Hesai Technology Showcases New Automotive-Grade Hybrid Solid-State Lidar AT128 at CES 2022
To summarize, the gap between camera-only, and LiDAR-plus-camera approaches is indeed diminishing, but I don’t believe that there will ever be a point where people feel like our camera-only cars are too safe for the additional cost of a LiDAR. I would be more than happy to see that day come, though.